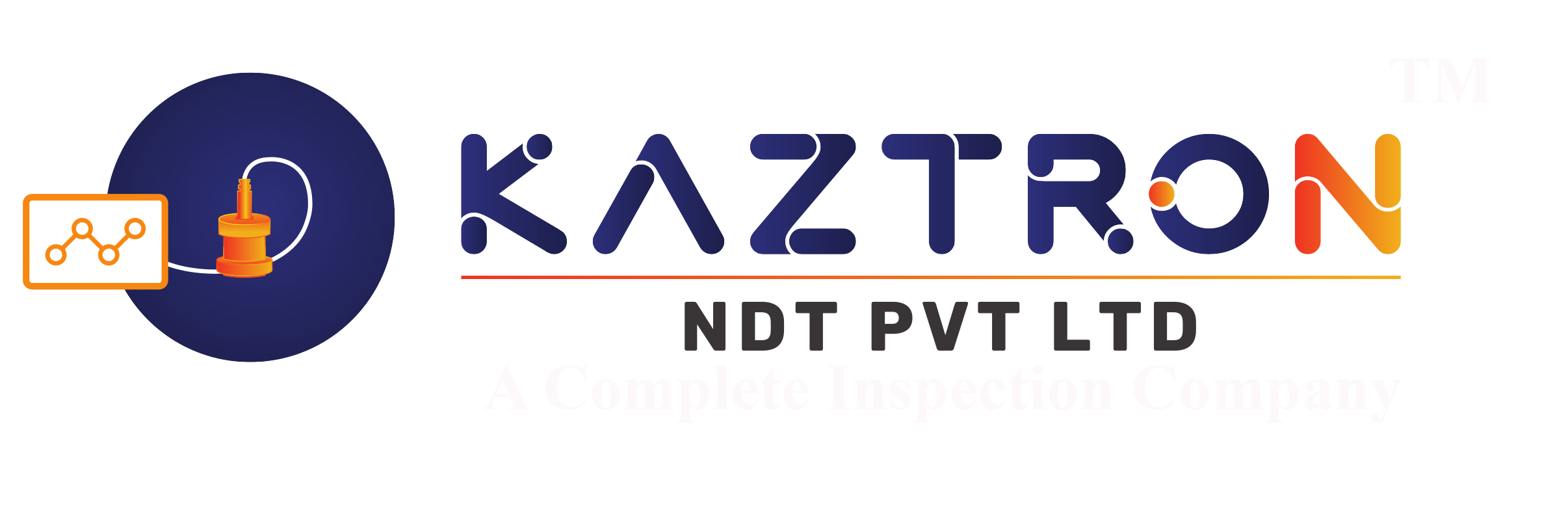
- +91-73564-85838
- [email protected]
Industrial radiography is a non-destructive testing (NDT) technique used to verify the internal structure and integrity of materials and components.
Industrial radiography is a method of non-destructive testing where many types of manufactured components can be examined to verify the internal structure and integrity of the specimen.
Industrial Radiographic Testing (RT) makes use of X-ray or gamma radiation to create images that can show defects hidden inside the material. This technology is widely used to ascertain material integrity of welds, castings, piping, machined parts, pressure vessels and other objects. The method is fully non-destructive and surface preparation of the test piece usually isn’t necessary. In many cases, RT can also be used to inspect industrial installations that are in operation.
Our Radiography Testing (RT) services ensure internal defect detection without damaging components. This method provides accurate, permanent records and is ideal for critical inspections across various industries—enhancing safety, reliability, and compliance. It reduces downtime, improves product quality, and supports preventive maintenance for long-term operational efficiency.
Radiography testing involves strict compliance with safety and accuracy standards.
Need help selecting the right RT technique or booking an inspection?
We ensure structural integrity and operational safety with cutting-edge Non-Destructive Testing services tailored for modern industries.
Our RT services detect internal flaws with high precision across diverse industries.
We’re trusted by major industrial clients for timely, accurate, and compliant NDT services.
Efficient inspection delivery across operational plants, pipelines, and fabrication yards.
From documentation to detection, our QA/QC workflow drives project excellence.
Industrial X-ray testing, also known as industrial radiography, is a non-destructive testing (NDT) method that uses X-rays to examine the internal structure of materials and components for defects. It allows for the detection of flaws such as cracks, porosity, and inclusions without causing any damage to the tested object. This technique is crucial for quality control, ensuring the integrity and reliability of various manufactured products and structures.
Benefits:
Explore answers to frequently asked questions about our Radiography Testing (Gamma Ray) services.
Detailed information on our RT Gamma services, safety protocols, inspection capabilities, and certifications can be found in the "Radiography Testing" section of our website. You can also request technical datasheets and case studies by contacting us directly.
Inspection reports for radiography testing are usually delivered within 24–48 hours after the site evaluation. In urgent or critical path scenarios, preliminary results may be shared on-site or on the same day, followed by the full report.
All RT Gamma inspections are carried out under strict safety standards. A controlled perimeter is set up during exposure, and only certified RT Level II or III technicians operate the equipment, ensuring compliance with regulatory guidelines.
Yes, in many cases, radiographic testing can be performed without halting operations. This depends on radiation shielding requirements and site access. Our team will assess feasibility during the initial survey.
Gamma radiography can detect internal flaws such as:
Porosity
Cracks
Inclusions
Lack of fusion
Misalignment in welds
It offers a clear view of both surface and sub-surface defects, making it ideal for weld joints, castings, and pressure vessels.
Yes. Both are forms of radiographic testing, but they differ in radiation source and application.
X-ray uses electrically generated radiation and is ideal for controlled environments.
Gamma Ray uses isotopes like Iridium-192 or Cobalt-60 and is more portable, making it suitable for fieldwork, pipelines, and remote inspections.
Each has its own strengths depending on material thickness, access, and inspection conditions.
Sign up our newsletter to get update news and article about company.
Kaztron NDT Pvt Ltd offers certified NDT training and inspection services, helping industries and professionals ensure safety, quality, and compliance through advanced testing techniques.